A
abraded yarn n. — a filament yarn in which one or more of its component filament fibers are cut and result in hairiness of the fiber (fibrillation), which may resemble a spun yarn.
abrasion, n. — a cluster of broken filaments (Syn: abrasion mark).
absorption, n. — the process whereby yarns or pores in fabrics transmit gases and liquids in the absence of a pressure differential; a process in which one material (the absorbent) takes in or absorbs another (the absorbate).
accelerated aging, n— in textile testing, the use of controlled environmental conditions to promote rapid physical or chemical change in a textile material.
acceptable quality level (AQL), n. — in acceptance sampling, the maximum fraction of nonconforming material at which the process average can be considered satisfactory; the process average above which the risk of rejection is called the producer’s risk.
acceptance number (c), n—in acceptance sampling, the maximum number of nonconforming items in a sample that allows the conclusion that the lot conforms to the specification.
acceptance sampling, n—sampling done to provide specimens for acceptance testing.
acceptance testing, n—testing performed to decide if a material meets acceptance criteria.
accuracy, n— for a test method, the degree of agreement between the true value of the property being tested (or an accepted standard value) and the average of many observations made according to the test method, preferably by many observers (See also bias and precision).
acetone, n. — dimethyl ketone (CH3COCH3); one of the most powerful organic solvents, capable of dissolving secondary cellulose acetate and other derivatives of cellulose, miscible with water, and having a low boiling point (55-60°C).
acidic, adj. — the chemical characteristic of a material having a pH of less than 7.0 in water.
acrylic, n. — synthetic textile fiber made by polymerization of acrylonitrile usually with other monomers; orlon.
adhesion, n. — the mechanical force that holds different materials together at their interface and which resists their separation; the property denoting the ability of a material to resist delamination or separation into two or more layers.
adhesion promoter, n. — chemical product used to treat the smooth fiber-face of a closely woven fabric to create a chemical bond site for subsequent coating or adhesive process, typically an isocyanite applied in a dip or contact coating operation.
adsorption, n. — the process in which the surface of a solid takes on or absorbs in an extremely thin layer molecules of gases, of dissolved substances, or of liquids with which it is in contact (See also absorption, moisture equilibrium of testing).
advanced composite, n. — polymer, resin, or other matrix –material system in which reinforcement is accomplished via high-strength, high-modulus, materials in continuous filament form or in discontinuous form such as staple fibers, fibrets, and in-situ dispersions.
afterflame , n. — in textile testing, the persistent flaming of a material after the ignition source has been removed.
after-flame time, n. — in textile testing, the length of time for which a material continues to flame after the ignition source has been removed.
afterglow, n. —the visual glow in a material after the removal of an external ignition source or after the cessation (natural or induced) of flaming of the material (See also flame, glow, and smoldering).
afterglow time, n. — the time afterglow continues after the cessation of flaming or after removal of the ignition source.
aftertreatment, n. — See Finishing.
alkaline, n. — the chemical characteristic of a material having a pH of more than 7.0 in water.
air entanglement, n. — the interlacing of filament fibers in a yarn bundle by means of air jets.
air permeability, n—the rate of air flow passing perpendicularly through a known area under a prescribed air pressure differential between the two surfaces of a material.
Discussion: Air permeability of fabric at a stated pressure differential between two surfaces of the fabric is generally expressed in SI units as cm 3/s/cm2 and in inch-pound units as ft3/min/ft 2 calculated in operating conditions.
air splice, n — the thicker portion of a yarn resulting from the entanglement of the filaments at the ends of two multifilament yarns to create a continuous yarn.
air texturing. n. — a process in which yarns are over-fed through a turbulent air stream so that entangled loops are formed in the filaments.
analysis of variance (ANOVA), n. — in statistical analysis of textile testing, the procedure for dividing the total variation of a set of data into two or more parts, one of which estimates the error due to selecting and testing specimens and the other part(s) estimates possible sources of additional variation.
anisotropic, adj. — not having the same properties in every direction.
antibacterial, adj. — relating to a fabric finish or yarn that acts to retard or stop the growth of bacteria.
ANOVA — See analysis of variance.
antistastic, adj. — relating to a chemical reagent, yarn property, or weave construction that disperses an electrostatic charge or prevents the buildup of static charge on a fabric or cut part.
aramid, adj. — a type of synthetic fiber in which the fiber-forming materials are a long chain polyamide having at least 85% of its amide linkages (—NH—CO—) directly attached to two aromatic rings.
Discussion: Aramid fibers exhibit low flammability, high strength, and high modulus. See also meta-aramid.
assignable cause, n. — in statistical analysis of textile testing, a contributing factor to variation that is feasible to detect and identify.
atmosphere for testing, n. — for textile testing, air at ambient conditions of relative humidity and temperature in which tests or experiments are conducted.
attribute , n. —a specific characteristic of a thing.
attribute data, n. —observed values or determinations which indicate the presence or absence of specific characteristics.
autoclave, n. — an apparatus, typically involving steam, that utilizes elevated pressures and temperatures for carrying out certain finishing operations, such as heat-setting of fibers and fabrics.
B
back side, n. — in textile materials, the side of the material that faces inward in the completed object (Ant: face side).
backed cloth, n. — a woven fabric with an extra layer of warp or fill yarns woven into the rear surface of the woven structure, making it a more 3-dimensional structure.
Discussion: Satin and twill weave constructions are often used in the design of backed cloth. Filling-backed fabrics permit the design of industrial fabrics for composite use in which the front layer of the fabric is dissimilar from the back surface. Double-face satin, on the other hand, employs two warps and one set of filling yarns to create two separate satin effects on each side of the fabric.
backing, n. — a general term for any weaving pattern which interlaces yarn on the back of the fabric.
baggy cloth, n. — a woven fabric that does not lie flat, commonly but not necessarily caused by tight warp yarns in the selvage.
baggy selvage, n. — See slack selvage.
basket weave, n. — a variation of the plain weave in which two or more warp and filling threads are woven side by side to resemble a plaited basket.
Discussion: Basket weaves exhibit a looser construction and exhibit a flatter appearance than an equivalent plain weave.
beam, n. — With a circular flange on each end, a cylinder on which warp yarns are wound for slashing and weaving.
beating up, n. — the next-to-last operation of the loom in the weaving cycle, in which the last-to-be-inserted fill yarn is rammed up against the preceding fill yarn(s), thereby tightly emplacing the yarn in an orthogonal configuration with respect to the warp yarns.
beck, n. — a vessel for dyeing fabric in rope form, consisting primarily of a tank and a reel to advance the fabric.
bending modulus, n. — for fabrics, the stress per unit of linear fiber weight required to produce a specified deflection of a fiber.
bias, n. — in conventional non-stretch fabrics, the orientation of a woven fabric 45°between the warp and fill that exhibits greater stretch than in either the warp of the fill direction alone.
bias fabric, n. — a fabric that has been reconstructed from conventionally woven fabric to exhibit bias stretch in the roll direction; a cut piece of fabric oriented in the bias direction.
bi-component fiber, n. — fiber spun from two different polymers.
Discussion: The most common types are made from polymers that have different melting points and are used for thermal bonding. Another variant is produced from polymers that have differing solubilities; in this case, one polymer may later be dissolved out to leave ultra-fine filaments, such as is done in the production of suede-like fabrics. This process is also be used to create crimping, to provide bulk or stretch.
bi-component yarn, n. — a yarn having two different continuous filament components.
bleedthrough, n —the presence of coating material on the uncoated side, between two yarns, without covering either yarn.
blip, n — any short, irregularly shaped or textured portion of an individual multifilament yarn that has been woven into the fabric, including slough offs, stripbacks, fuzz balls, snarls, and slubs.
blocking, n. — for coated fabric, an undesired adhesion between adjacent layers of material, such as occurs under moderate pressure within a roll of coated fabric.
blotch, n. — an irregularly shaped off-colored area.
bow, n. — a fabric condition resulting when filling yarns or knitted courses are displaced from a line perpendicular to the selvages and form one or more arcs across the width of the fabric.
braid, n. — a narrow tubular or flat fabric produced by intertwining a single set of yarns according to a definite pattern.
braided fabric, n. — a structure produced by interlacing three or more ends of yarns in a manner such that the paths of the yarns are diagonal to the vertical axis of the fabric.
breaking force, n. — the maximum force applied to a material carried to rupture.
breaking point, n. — in textile testing on a force-extension or force-elongation curve or on a stress-strain curve, the point corresponding with the breaking force or the breaking stress in a tensile test.
breaking strength, n. — the ability or capacity of a specific material to withstand the ultimate tensile load or force required for rupture.
breaking tenacity, n. — the tenacity at the breaking force.
breathability, n. — the ability of a fabric, coating, or laminate to transfer water vapor from one of its surfaces through the material to the other surface. See also moisture vapor transmission rate (MVTR).
broken end, n. — in woven fabrics, a void in the warp direction due to yarn breakage.
broken filament, n. — in multifilament yarn, breaks in one or more filaments; an individual filament, separated from a multifilament yarn bundle, that lies on the surface of the fabric.
broken pick, n. — in woven fabrics, a discontinuity in the filling direction caused by a break or cut in the filling yarn.
broken twill, n. — a twill weave in which the twill line changes direction.
bruise, n — a shift in the squareness of the weave pattern in an area that appears different from surrounding fabric and appears to have been subjected to impact or pressure.
bursting force, n. — the force or pressure required to rupture a fabric by distending it with a force, applied at right angles to the plane of the fabric, under specified conditions.
bursting strength, n. — in textile testing, the capacity of a textile specimen to withstand the ultimate bursting force required to rupture it.
C
cationic dye, n. — a dye that dissociates in aqueous solution to give a positively charged colored ion.
char, v. — to form carbonaceous residue as the result of pyrolysis or incomplete combustion; to form char or charring.
clip mark, n. — in fabric inspection, a visible deformation near the edge of a fabric parallel with the lengthwise direction caused by pressure exerted by a clasping device on a clip tenter frame (See also pin mark).
coated fabric, n. — a flexible material composed of a fabric and any adherent polymeric material applied to one or both surfaces.
coating, n. — application of liquid adherent material, such as an elastomer, to the surface of the fabric by dipping, spraying, brushing, calendering or knife coating to alter the physical properties or appearance of the fabric.
coating slub, n — an irregularly shaped lump of coating material on the surface of the coated layer resembling a yarn slub.
coating streak, n — minor variation in the color or opacity of a coated layer.
coating transfer, n — in coated fabrics, the unintended presence of coating material on the uncoated side, covering one or more yarns.
coefficient of friction, n. — the ratio of the tangential force that is needed to maintain uniform relative motion between two contacting surfaces to the perpendicular force holding them in contact.
coefficient of variation, CV, n. — a measure of the dispersion of observed values equal to the standard deviation for the values divided by the average of the values; may be expressed as a percentage of the average (CV %).
cloth beam, n. — a cylinder with flanges located at the front of the loom, onto which the woven cloth winds.
color bleeding, n. — the loss of color from a dyed fabric when immersed in water, drycleaning solvent, or similar liquid medium, with consequent coloring of the liquid medium (Compare color staining, crocking).
color grading, n. — the act of identifying a specimen by a color grade or color score that is specific to the color and the material graded.
colorfastness, n. — the resistance of a material to change in any of its color characteristics, to transfer its colorant(s) to adjacent materials, or both, as the result of exposure of the material to any real or simulated environment that might be encountered during processing, storage, use or testing of the material.
combustion, n. — a chemical process of oxidation that occurs at a rate fast enough to produce heat and usually light either as glow or flames.
condition, v. — to bring a material to moisture equilibrium with a specified atmosphere.
constant-rate-of-extension type tensile testing machine (CRE), n. — a testing machine in which the rate of increase of specimen length is uniform with time.
constant-rate-of-extension type tensile testing machine (CRE), n. — in tensile testing, an apparatus in which the pulling clamp moves at a uniform rate, and the force-measuring mechanism moves a negligible distance with increasing force, less than 0.13 mm (0.005 in).
constant-rate-of-traverse tensile testing machine (CRT), n. — in tensile testing, an apparatus in which the pulling clamp moves at a uniform rate and the force is applied through the other clamp which moves appreciably to actuate a weighing mechanism, so that the rate of increase of force or extension that is usually not constant and is dependent upon the extension characteristics of the specimen.
contamination, n — for uncoated fabrics, the presence of material in the fabric not of the same composition as the fiber(s) designed to be woven into the fabric; for coated fabrics, the presence of non-coating material in a coated layer.
control limits, n. — predetermined ranges based on the variability of past observations between which the instrument data for a test must fall to be considered valid.
count, n. — in woven textiles, the number of warp yarns (ends) and filling yarns (picks) per unit distance as counted while the fabric is held under zero tension, and is free of folds and wrinkles.
course, n. — in knitted fabrics, a row of successive loops in the width direction of the fabric.
crease, n. — a fabric imperfection evidenced by a line in a fabric evidently caused by a sharp fold.
crease mark, n. — a visible deformation left in a fabric after a crease has been incompletely removed during fabric processing.
crimp, n. — in a textile strand, the undulations, waviness, or succession of bend, curls, or waves in the strand induced either naturally, mechanically, or chemically.
Discussion: Crimp has many characteristics, among which are its amplitude, frequency, index, and type.
crocking, n. — a transfer of color from the surface of a colored fabric to an adjacent area of the same fabric or to another surface principally by rubbing action (Compare to color bleeding).
cross-dye effect, n. — variation in dye pick-up between yarns or fibers, resulting from their inherently differing dye affinities.
crowfoot weave, n. — in weave construction, a broken-twill weave 1-up and 3-down or 3-up and 1-down with two ends to the right and two ends to the left, commonly referred to as four-harness satin or broken crow.
D
defect, n — an imperfection in a cut piece of fabric that judgment and experience indicate is likely to result in either improper or hazardous operation or performance of the final product in which the imperfection is incorporated (Compare to imperfection).
Discussion: An example of a defect is a hole in the piece of fabric through which gases on one side of the fabric can vent improperly or unintentionally to the reverse side.
denier, n. (den’ yer") — 1) the weight-per-unit-length measure of any linear material; 2) for filament yarns, a unit of fineness equal to the fineness of a yarn weighing one gram for each 9000 meters.
Discussion: Denier is a direct numbering system in which the lower numbers represent the finer sizes and the higher numbers the coarser sizes. In the U.S., the denier system is used for numbering filament yarns (except fiberglass). In most countries outside the U.S., the tex system is used.
direct yarn numbering system, n. — a system of yarn comparison that expresses the linear density of yarn in mass per unit length.
Discussion: The preferred units of measurements for the direct yarn measuring system are grams and meters. Tex (weight in grams for 1000 meters) and Denier (weight in grams for 9000 meters) are recommended to show linear density in the direct numbering system.
direction of twist, n. — the right or left direction of the helix formed in a twisted strand as indicated by superimposition of the capital letter “S” or “Z”.
discrete production, n. — type of manufacture that produces components that are distinctly separate from one another and that lend themselves to easy statistical analysis; discrete component production (Compare to continuous production).
distortion, n. — in fabric inspection, a unintended and visible alteration in a portion of the texture of a fabric, from many sources including snags and bruises.
dobby, n. — a mechanism applied to a loom that enables weaves and patterns to be produced that cannot be obtained on a tappet loom, but are much less elaborate than those obtained by Jacquard weaving; fabrics woven on such equipped looms.
double-face satin, n. — a satin weave construction employing two warps and one set of filling yarns to create two separate satin effects on each side of the fabric.
double pick, n. — in woven fabrics, two picks wrongly woven together as one.
dye streak, n. — an unintended stripe in a fabric due to uneven absorption of a colorant.
dyestain, n. — an area of discoloration due to uneven absorption of a colorant.
E
eight-harness satin, n. — in woven fabric design, a warp-faced or filling-faced weave illustrating that the entire face of the fabric surface is covered with warp or filling yarn, respectively.
elongation, n. —the ratio of the extension of a material to the length of the material prior to stretching, expressed as a percent (Compare extension).
elongation at break, n. —the elongation corresponding to the breaking force (Compare elongation at rupture. See also elongation).
elongation at breaking load, n. — in fiber strength testing of cotton, the elongation corresponding to the maximum load, and expressed as a percentage of the 1/8-in. (3.2-mm) gage length.
elongation at rupture, n. — the elongation corresponding to the force-at-rupture (Compare elongation at break).
elongation at specified force, (EASF), n. — the elongation associated with a specified force on the force-extension curve.
embrittlement, n. — the formation of a brittle residue as the result of pyrolysis or incomplete combustion.
end, n. — in fabric , an individual warp yarn (single or ply) or cord; a short length or remnant of fabric.
end out, n. — a void caused by a missing warp yarn.
entanglement, n. — the extent or degree to which the filaments in a yarn are interlocked and cannot be readily separated.
environmental conditions, n. — in textile testing, the atmosphere in which specified moisture levels, temperature ranges, and concentrations of gases are controlled.
examination, n. — in fabrics, the visual inspection of the condition of a roll of fabric or of a cut piece of fabric, and the comparison of the fabric condition to an agreed-upon standard for imperfections and/or color.
F
fill, n. — in a woven fabric, the yarn running from selvage to selvage at right angles to the warp, each crosswise length being called a pick; also woof, weft, or transverse.
Discussion: In the weaving process, the fill yarn is carried across by means of a shuttle, a rapier (rigid or flexible), or a jet of air or water.
filling bar, n — a temporary change in the filling-wise density of the weave pattern (Syn: stop/start mark).
finished, adj — a descriptive term for fabric that has been treated after weaving in and that is suitable for coating or piece cutting.
FOB, n. — Freight on Board; the point at which ownership and insurance responsibility of the merchandise changes from producer to customer.
foreign matter, n — an extraneous interwoven fragment whose size, color, or texture indicates that it is not of the same material as the fibers in the base fabric.
G
grading, n — the procedure used to identify and quantify the number of imperfections in a roll of fabric detected during visual inspection.
grey cloth, n. — a term synonymous with ‘loomstate’ which refers to the condition in which the woven cloth leaves the loom.
H
hole, n — an opening not characteristic of the normal weave pattern where one or more yarns is cut, torn, or shifted.
I
imperfection, n — a departure of a quality characteristic from its intended level or state.
inspection, n — the process of viewing, measuring, examining, or otherwise comparing the visual characteristics of a fabric with applicable requirements.
J
jacquard, n. — fabric woven with a large scale repeat requiring a mechanically controlled mechanism (the Jacquard mechanism) to select and lift individual warp yarns while weaving; such mechanism capable often a more complex weave than a dobby or tappet loom.
K
knitting, n. — a method of converting yarn into cloth using parallel courses of yarn, each course being joined to another by interlocking loops in which a short loop of one course of yarn is wrapped over or through that of another course.
L
leno, n.: — a cellular type of cloth made by crossing warp threads in weaving.
long float, n — a small change in the weave pattern where a warp or filling yarn extends over six or more filling or warp yarns with which it should be interlaced.
loom, n — Machine designed to interlace warp and fill yarns to produce woven fabric.
loop, n — a continuous yarn that curls back on itself and protrudes from the surface of the fabri. (Syn. kink, snag).
lycra, n — a man-made fiber with elastane properties manufactured by Dupont.
M
major imperfection, n. — in fabric grading, a deviation in a roll of fabric that judgment and experience indicate is likely to have an adverse affect on subsequent use or processing of the fabric.
Discussion: Examples of major imperfections are a yarn loop that could become snagged and a fabric stain that could affect the physical properties of the material.
marquisette, n. — a lightweight leno gauze.
minor imperfection, n — in fabric grading, a deviation in a roll of fabric that judgment and experience indicate is likely to have no bearing on subsequent use or processing of the fabric.
Discussion: Examples of minor imperfections are a seam mark and a stop/start mark.
missing coating, n. — portions of a coated layer containing exposed base fabric or scrape marks in the coated layer.
missing yarn, n. — a yarn discontinuity resulting in a change in weave pattern.
misweave, n. — a change in the weave pattern caused by incorrect interlacing or insertion of a yar (Includes mispick, wrong draw, jerk-in).
mock leno, n. — a cellular type cloth in which spaces develop between groups of threads to resemble a leno weave without crossing warp yarns.
MVTR, n. — moisture vapor transmission rate; measurement of breathability.
N
narrow fabric, n. — woven textile fabric not exceeding 45 cm in width with 2 selvedges; narrow woven; smallwares.
nonwoven, n. — a sheet, web, or batt of natural and/or man-made fibers or filaments, excluding paper, that have not been converted into yarns, and that are bonded to each other by several means, such as chemical adhesion (glueing), thermal bonding (melting), stitching, and entanglement.
Discussion: Nonwovens are usually the cheapest method of creating a matrix of yarns, followed by knitting, and lastly by weaving. They are also the least predictable of the three methods in terms of achieving tight tolerance, high performance textiles because, at the very least, the fibers are emplaced in random order.
O
olefin, n. — manufactured fiber in which the fiber-forming substance is any long-chain synthetic polymer composed of at least 85% by weight of ethylene, propylene, or other olefin units; a generic description that covers thermoplastic fibers derived from olefins, predominately aliphatic hydrocarbons, that are products of the polymerization of propylene and ethylene gases, polypropylene (PP) and polyethylene (PE) being the two most common members of the family.
olive drab, adj. — a grayish olive color usually associated with military fabric.
one-piece woven, adj — a descriptive related to a tubularly woven fabric composed of two-layer sections that are separable, woven sections that are non-separable, and visible lines where the two layers initially interlace.
Discussion: Under certain designs, a weaving machine is capable of simultaneously weaving two separate layers of fabric, one over the other, with tight interlacings selectively woven between them. Where the layers are not interlaced, the fabric is capable of being inflated; where they are interlaced, inflation is not possible. Although the pattern in the fabric described by the visible line where the two inflatable layers interlace may be a complex shape other than a tube, the construction is commonly referred to as tubularly woven.
P
permeability, n. — in fabric testing, the property of a material to transmit a gas, usually air, at a fixed pressure differential, measured in units of linearity per minute.
Discussion: Permeability can assist the determination of the expected performance of the wind resistance of a sailcloth, the rate of descent of a parachute, or the flow or gases or liquids through a filter.
piece, n. — an arbitrary unit length of fabric removed from a loom.
Discussion: Piece length depends on many limiting factors such as fabric weight, loom geometry, finishing limitations, and end-user requirements. According to the state of the cloth, expressions such as “loomstate piece” and ‘dyed piece’ may be used.
plain weave, n. — weave pattern made by weaving one weft yarn over and under each warp yarn, alternating each row.
Discussion: The plain weave is the most common type of weave.
producer’s risk, n. — in acceptance sampling , the fractional portion of the process average of nonconforming material at or above which material is considered unacceptable for shipment by the producer.
Q
R
rayon, n. — manufactured fiber composed of regenerated cellulose in which substituents have replaced not more than 15 percent of the hydrogens of the hydroxyl group; viscose.
rework, n. — the deviation from normal process flow remedially altering finished fabric, coated fabric, or cut pieces for the purpose of minimizing or removing an imperfection.
S
sateen, n. — A weft-faced cloth made in one of the sateen weaves, usually with many more picks than ends, and finished to improve the cover and luster.
satin weave, n — the weave pattern made by “floating” the warp or weft yarns across several yarns to bring them to the surface.,
Discussion: One effect of the floating yarns is surface sheen because light is reflected off the yarn surface, not absorbed by the more frequent intersections of yarns of a plain weave. Satin weaves are common in fabrics used in composite layups because the surface provides a greater exposure of the yarn for mechanical adhesion of resin.
scrim: A loosely constructed open lightweight woven fabric.
selvage, n. — the narrow edge of woven fabric that runs parallel to the warp. It is made with stronger yarns in a tighter construction than the body of the fabric to prevent raveling. A fast selvage encloses all or part of the picks, and a selvage is not fast when the filling threads are cut at the fabric edge after every pick (selvedge).
sharp crease, n — a sharp ridge that can be felt easily, caused by a hard folding of the fabric over itself not by design.
short float, n — a warp or filling yarn extending over five or fewer filling or warp yarns with which it should be interlaced.
short knot, n. — a small knob of yarn and associated tails where two yarns are tied together by interlocking loops for the purpose of maintaining yarn continuity.
spit mark, n. — for coated fabrics, an essentially round spot of coating material on the surface of the coated layer.
spun yarn, n. — a textile yarn made from staple-length fiber using a spinning method of entanglement.
Discussion: The relative size of spun yarns is determined by the indirect yarn number system.
stain, n. — an area of discoloration that penetrates the fabric surface.
stick-slip, n. — in tribology, a relaxation oscillation usually associated with decrease in the coefficient of friction as the relative velocity increases; a cyclic fluctuation in the magnitudes of frictional force and relative velocity between two elements in sliding contact, usually associated with a relaxation oscillation dependent on a decrease of the coefficient of friction with the onset of sliding motion or with an increase in sliding velocity.
Discussion: The classical or true stick-slip in linear or rotational guideways occurs when a stage of actual stick is followed by a stage of overshoot “slip;” this requires that the static coefficient of friction be higher than the kinetic (or dynamic) coefficient. A modified form of relaxation oscillation, with near-harmonic fluctuation in motion, can occur when the kinetic coefficient of friction decreases gradually with increasing velocity within a certain velocity range. A third type of stick-slip can be due to spatial periodicity of the friction coefficient along the path of contact. Random variations in frictional force measurements do not constitute stick-slip.
T
taffeta, n. — a warp-oriented woven fabric characterized by indistinct warp ribs from using yarns of equal thickness in both warp and weft but having many more ends than picks, resulting in a stiff plain weave construction.
tensile strength, n. — 1) generally, the strength shown by a specimen subjected to tension as distinct from torsion, compression, or shear; 2) in woven fabrics, the maximum tensile stress expressed in force per unit cross-sectional area of the unstrained specimen, e.g., kilograms per square millimeter, pounds per square inch.
tensile tester, n. — a high precision electronic test instrument designed for measuring and charting the load-elongation, tear resistance and resistance to compression properties of fibers, yarns, and fabrics under a broad range of test conditions.
tenacity, n. — the tensile stress when expressed as force per unit linear density of the unstrained specimen (e.g., grams-force per denier or newtons per tex).
tex, n. — 1) unit of measurement for expressing liner density, equal to the weight in grams of 1 kilometer of yarn; 2) the system of yarn numbering based on the use of tex units.
thread count, n. — in a woven fabric, the measurement of the number of warp ends per inch and filling picks per inch.
tight yarn, n. — a yarn with less crimp than surrounding fibers that may create puckering, which may appear to be shinier or to lie straighter in the weave pattern, or a combination thereof.
tricot, n. — a plain warp-knitted fabric with a close, relatively inelastic knit used especially occasionally for inexpensive substrates.
twill weave, n. — a weave pattern similar to a satin weave in that yarns in one direction float over yarns in the other (orthogonal) direction, in a manner that creates distinctive, diagonal lines in the fabric.
Discussion: A twill weave is more supple than an equivalent plain weave pattern, which is useful for protective apparel in terms of comfort and durability; it is is also used in composites to increase resin adhesion.
U
urethane, n. — designation for a group of organic chemical compounds or resins built from isocyanate, a very reactive-material that liberates gas during reaction with polyesters and polyethers to produce foams of various types.
V
W
warp, n. — 1) in all woven fabrics, the set of yarns that runs lengthwise and parallel to the selvage, and that is interwoven with the filling; 2) the sheet of yarns wound together on a beam for the purpose of weaving or warp knitting.
warp knit, n. — a knit fabric with the yarns running in a lengthwise direction and sometimes used as an inexpensive substrate material.
weaving , n. — the process of interlacing warp and weft yarns in a predetermined pattern to create a woven fabric.
weft, n. — in English textile vernacular, the yarn applied orthogonal to the warp in a certain pattern during weaving to achieve a predetermined pattern; fill.
weft knit, n. — a knit fabric with the yarns running crosswise or in a circle.
X
yarn, n. — a continuous strand of fiber spun from a group of natural or synthetic staple fibers or filaments, used in weaving or knitting.
Discussion: Yarns are made up of any number of plies, each ply being a single thread, twisted (plied) together to make the final yarn. In some cases, yarn may be monofilament, in which case it is a single fiber; the only natural fiber that is counted as monofilament is silk. Yarn is manufactured by either a spinning or air texturizing (commonly referred to as taslanizing) process.
yarn dyed, adj. — condition of yarn prior to weaving, the color imparted by dyeing skeins of yarn or directly adding color in the polymer state prior to extrusion.
yarn number, n. — the relative measure of the fineness of yarns.
Discussion: There are two yarn number systems in use, direct and indirect. The direct yarn number (equal to linear density) is the mass per unit length of yarn; this is used for manufactured filament yarns. The indirect yarn number (equal to the reciprocal of linear density) is the length per unit mass of yarn; this system is used for spun yarns and fiberglass.
yarn streak, n. — discoloration of an individual yarn that does not affect adjacent yarns.
Z
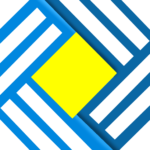